Freeze Drying Processes
The main freeze drying processes are:
- Drying in round-bottom flasks, wide-neck filter bottles, ampoules, etc. (double-chamber method). The product is pre-frozen externally in a freezer or a cooling bath and then connected to the freeze dryer through a three-way rubber valve. Each vessel can be attached and removed individually.
- Drying products in dishes, vials or similar containers on shelves (in some cases heatable) outside the ice condenser chamber (double-chamber method). The product is pre-frozen externally in a freezer or a chilling bath and then dried under an acrylic or stainless steel cover. Removing individual specimens during the process is not recommended (risk of thawing).
- Freezing and drying in dishes, vials or similar containers inside the ice condenser chamber (single-chamber method). In this case the entire process can be carried out inside the unit without additional product handling and be fully automated if necessary. Freezing results from chilled air (convection), possibly accelerated by forced air circulation with a fan. Particularly recommended for expensive and/or sensitive products (low freezing point < –25 °C)
- Freezing and drying in dishes, vials or similar containers on cooled and heated shelves. Here as well the entire process can be carried out fully automatically inside the drying chamber without additional product handling. Freezing results from direct contact with the cold shelf (conduction). Standard method at production scale and in pilot systems for process development or optimisation.
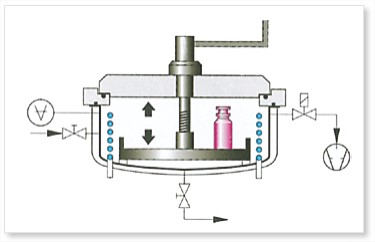
Single-chamber method
With this configuration the product is frozen inside the ice condenser chamber and then dried. This method is particularly suitable for substances with low freezing points or thermally unstable substances. In this method, the shelves are located directly in the ice condenser chamber. Freezing can also be assisted by a fan. A stoppering device for vials may optionally be used.
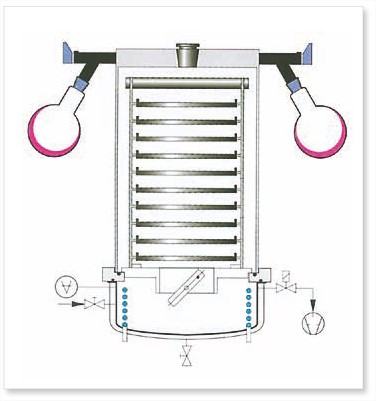
Double-chamber method
With this configuration the product is separately pre-frozen and then dried above the ice condenser chamber. This method allows a large variety of accessories to be used. An intermediate valve can be used to separate the product chamber from the ice condenser chamber for the pressure increase test to determine the drying endpoint.